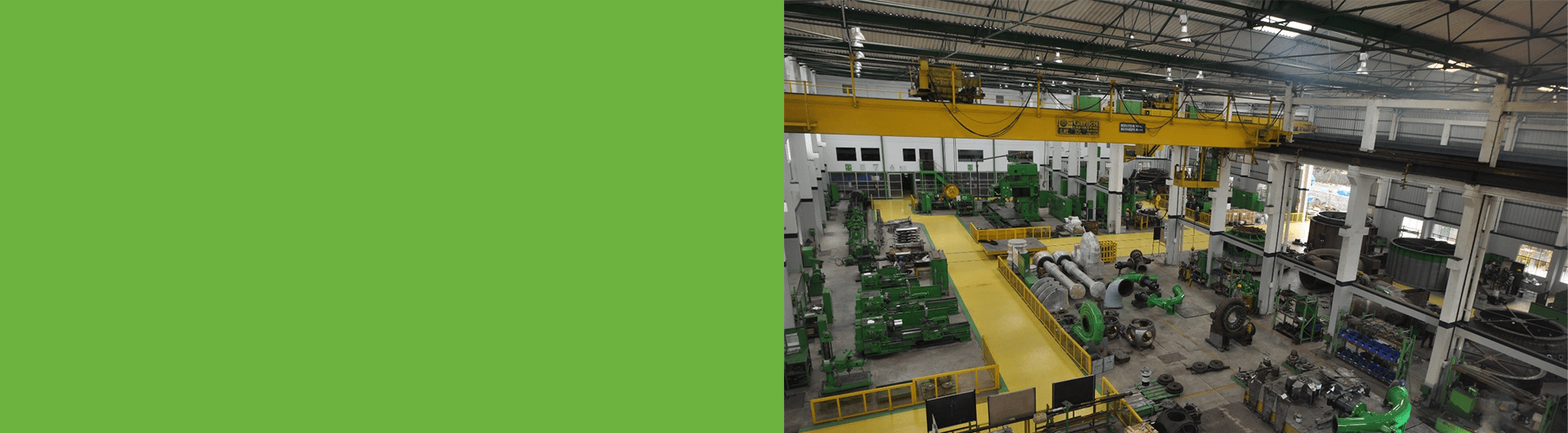
Delivering
Excellence
Focus on Quality & Precision
Continuous Improvement Programs (CIP) and Total Quality
Management(TQM) is the key to our success
BFL Manufacturing System – Delivering Excellence:
Lean Manufacturing System, being the core process of our Manufacturing Principles, is an amalgamation of Process, Technology, Plant, Machineries, Systems and Work force. Continuous Improvement Programs (CIP) and Total Quality Management(TQM) is the key to our success, for delivering High Quality products (comparable to International standards) to our customers in India and abroad.
BFL Manufacturing Plant at Hoskote (Bangalore, India) is spread across 10 acres property in lush green surrounding. The Plant meets high environmental and Safety standards and are a certified “ISO 9001:2015”, certified company.
BFL’s Hoskote Plant puts everything under one roof - that is needed for Manufacturing and testing of all types/configuration of Turbines, up to 30MW capacity. Our Manufacturing set up has following facilities:
Machine Shop:
We have high precision Multi-Axes CNC Lathe and Milling machines, to produce the core component of turbines like Guide Vanes, Runner, Runner Blades, Rotating Hub, Bearing components etc. All such key components go through stringent manufacturing process and quality checks there by ensuring long lasting and trouble free operation of our products. Our machine shop can handle components up to 6 meter diameter.
Fabrication and Welding shop:
Is well equipped with Multi Axes Welding Manipulator having TIG/MIG/Arc welding facilities. 100% of our welders are qualified and certified welders, by the competent authority. We have, in house facilities/Manpower, for conducting tests on weld joints like UT, MPT and DPT.
Assembly and Testing:
All our turbines are completely assembled to the last bolt and nut, before getting dispatched to the site. All types of ‘assembly clearance’ and ‘alignment checks’ are performed on the test bed. We invite our esteemed Customers to witness the same. We have 2 nos Assembly bays with test rigs for assembly and Testing of Turbine.
Manufacturing Innovation:
3D Printed Casting: We are proud to announce that, we have successfully developed and implemented the 3D Printing technology for production of Francis runner castings. We have already supplied such runners to our customers across the globe.
Quality at every step:
The BFL plant is ISO9001: 2015 certified. We follow Lean Manufacturing principles in the shop floor and ours is a 5S Enabled plant. We have stringent quality checks at every step, right from the receipt of material to the final assemblies. Our Quality Management System takes care of all process steps which are documented and reviewed by our experienced team of Engineers. In our company, we have cultivated a culture of quality that permeates everything we do. Our manufacturing team works relentlessly on process improvement, cost reduction and a multitude of other improvement opportunities to deliver the highest levels of quality, value and service to our customers.
Our Supplier Base – The Committed Partners:
At BFL, we consider suppliers as our partners in our drive towards excellence. All our suppliers are continuously evaluated and trained on our requirements. We source raw material like casting, forging etc from the renowned suppliers in the Hydro field. Similarly, all the small components (like hardware, seals, fasteners etc) are sourced from the best in class in the industry.
Packing and Documentation:
We understand the importance of packing and we follow international standard of packing for our ocean and land transport. Customized solutions are the key to our success. Documentation plays a critical role in ensuring the future quality of the solutions BFL delivers. To enable traceability for raw material and heat treatment, mill certificates and all relevant inspection records are maintained for every turbine component.